Case study: Automotive components
Engineering giant Marelli streamlines supply chain to cut cost and reduce its environmental impact
With the aim or reducing cost and streamlining its supply chain management whilst reducing environmental impact, Marelli are seeing the benefits of partnering with Enviroquip and Forward.
In 2019 Calsonic Kansei and Magneti Marelli united to create the global brand Marelli combining the best of Italian and Japanese engineering heritage. Its footprint now includes 170 manufacturing, R&D and distribution centres around the world, employing around 54,000 people.
At Marelli Automotive Systems, a dedicated staff of 300 manufacture and test air conditioning units, compressors and heat exchange products for OEM brands including Range Rover, Audit and Nissan supporting production lines in the UK, Germany and Slovakia.
“We needed to reduce the cost of waste management and single source to streamline management”
With the aim of improving operational effectiveness, reducing cost and carbon, across multiple manufacturing sites in the UK, Hydro is seeing the impact of implementing bespoke waste handling equipment from Enviroquip combined with a total waste management service from Forward Waste.
Market Sector: Automotive component manufacturing
Locations: Carmarthenshire
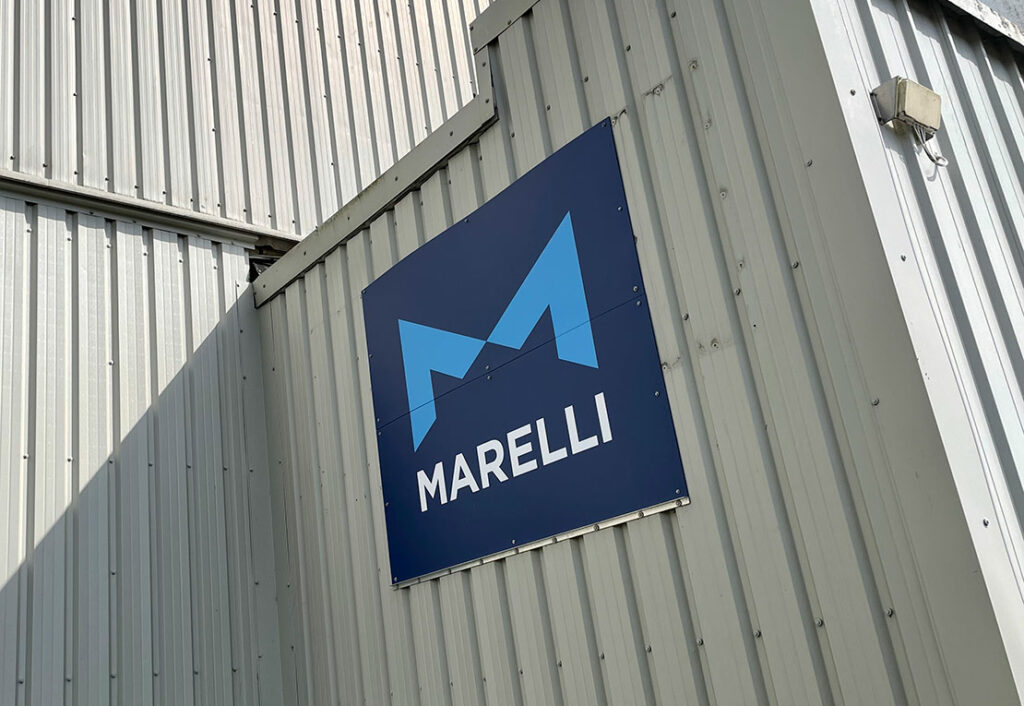
“The equipment is in much better condition, more trustworthy. It has a larger capacity, 13% bigger. Truck movements are reduced so vehicle emissions are reduced. We’re measuring the impact. ”
Ian Williams, Environmental, Health & Safety Engineer, Marelli Automotive Systems
Customer Benefits

Cost reduction

Environmental best practice
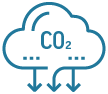
Carbon reduction
Customer challenge
Marelli wanted to improve recycling levels, reduce risk, mitigate cost, and streamline their supply chain. They wanted to improve the performance and reliability of waste handling equipment on-site, and to have greater confidence in its waste and resource arrangements that underpin it’s committment to Zero to Landfill.
Waste streams to manage:
- general waste
- scrap timber
- cardboard
- nylon and polypropylene moulding scrap
- spent shot blast media
- gas filled nylon moulding scrap
- packaged hazardous waste
- Bulk caustic waste
Our approach
An integrated solution combines waste segregation bins, baling system, and upgraded compactor and larger capacity containers. This equipment solution from Enviroquip combines with a total waste management service from Forward.
Enviroquip waste handling equipment solutions:
- heavy duty static compactor with bin lift system
- mill size vertical baler producing European specification 500 kg bales
- colour-coded and labelled wheelie bins
Our customer impact
- Increased waste segregation and reduced general waste
- Improved health, safety and hygiene conditions
- Improved team morale through provision of modern, reliable equipment with training certificates
- Carbon reduction
- Confidence in Zero to Landfill
- Single accountability for all environmental services and equipment
- Cost reduction in line with forecasts
“ I’m a time-served engineer. I could see that the quality of manufacturing was first class. My standards are high. I’m looking for quality.”
Ian Williams, Environmental, Health & Safety Engineer, Marelli Automotive Systems